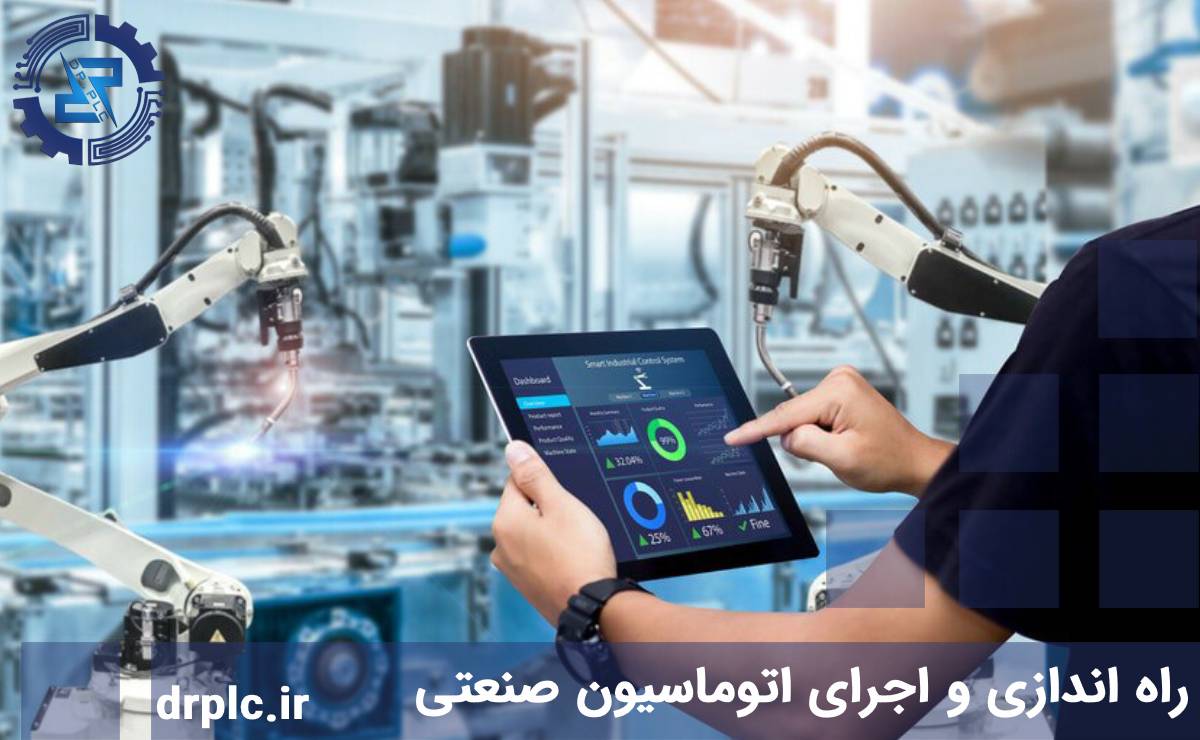
خدمات راه اندازی و اجرای اتوماسیون صنعتی
اکنون، اتوماسیون صنعتی باعث بهبود کارایی فرآیندهای تولیدی شده و تحولات مثبتی را در دنیای صنعت ایجاد کرده است. اما، این پیشرفت همراه با نگرانیهای فراوانی درباره تأثیرات آن بر مهارتها، اشتغال و بیکاری نیز رقم زده است. به کارگیری فناوریها و ماشینآلات به منظور اتوماسیون، انجام وظایف را بدون نیاز به حضور فعال انسان را ممکن میسازد.
بطور کلی، اتوماسیون را میتوان به کنترل پروسهها با استفاده از تجهیزات الکترونیکی، ماشینها و سیستمهای کامپیوتری با حداقل دخالت انسان تعریف کرد. در اتوماسیون صنعتی، فرایندها به وسیله برنامههای کنترلی و دستورالعملها، بدون نیاز به مداخله انسانی، به اجرا در میآیند. امروزه این تکنولوژی در تمام جنبههای صنعت، از ساخت و تولید تا نصب و نگهداری، به صورت کاملاً اتوماتیک مورد استفاده قرار میگیرد.
مراحل اجرای یک پروژه اتوماسیون صنعتی
اتوماسیون صنعتی در یک کارخانه یا فرآیند صنعتی، از مراحل متعددی طراحی، تأمین کالا، برنامهنویسی، راهاندازی و ... تشکیل شده است. امروزه، با پیشرفت گسترده در صنایع مختلف و رقابت فراوان بین انواع کارخانجات تولیدی و صنعتی، ضرورت استفاده از دستگاههای نوین احساس میشود. این دستگاهها باید قادر باشند محصولات را با کیفیت بالاتر تولید کرده و به همراه کاهش هزینههای تولید، همچنین کاهش احتمال خطاهای انسانی، عمل کنند. این نیاز به دلیل رشد فناوری و پیشرفتهای صنعتی بیش از پیش اهمیت یافته است.
در ادامه تلاش شده مراحل اجرای اتوماسیون صنعتی با دیدگاه کاملاً عملیاتی و مطابق بر استاندارد های روز که نتیجه طراحی و اجرای پروژهای بیشمار اتوماسیون صنعتی توسط دکتر پی ال سی بوده شرح داده شود.
1) دریافت درخواست مشتری
مرحله ابتدایی در انجام پروژههای اتوماسیون صنعتی، دریافت درخواست از مشتری میباشد؛ زیرا وجود یک درخواست ضروری است تا بتوان به بهترین شکل ممکن با راهحلهای مهندسی، نیازهای مشتری را پاسخ داد. در این مرحله، ابتدا نیازمندی های مشتری را بررسی میکنیم. این اطلاعات اساسی هستند تا بتوانیم با ارائه راهکارهای اتوماسیون صنعتی مناسب، به بهبود نیازهای مشتریان پرداخته و پروژه را به اجرای موفق برسانیم.
2) مشاوره و ارزیابی های اولیه
در این مرحله، هماهنگی بین کارفرما، مشاوران، و متخصصین دکتر پی ال سی انجام میشود و لازم است اطلاعات ابتدایی مرتبط با پروژه مورد نظر کارفرما به دست مشاوران برسد. سپس آنها با استناد به دانش و تجربیات خود، سعی میکنند به کارفرما راهنمایی کنند تا به اهداف خود دست یابد.دکتر پی ال سی ابزارهای نرمافزاری و سختافزاری مناسب را به کارفرما پیشنهاد میدهد تا نیازها و مسائل کارفرما را به بهترین شکل ممکن حل نماید.
قبل از ارائه مشاوره دقیق در زمینه اتوماسیون صنعتی، مشاوران و متخصصان نیاز به دریافت اطلاعات از فرآیندها در کارخانه دارند. این اطلاعات را باید کارفرما قبل از شروع برآوردها ، به گروه مشاوره دکتر پی ال سی ارائه کند. برخی از مستندات و مدارک عبارتند از :
- نقشه فلو پروسه Flow Diagram (PFD)
- نقشه های P&ID
- لیست موتورها
- لیست سنسورها و ابزاردقیق
- لیست شیرها و عملگرها
- و …
3) بازدید حضوری
بعد از دریافت اطلاعات و مستندات اولیه از فرآیندها، مرحله بعدی این است که مهندسان و متخصیین دکتر پی ال سی به صورت حضوری از خطوط تولید و تجهیزات بازدید کنند. این بازدید ضروری است زیرا به هر اندازه که مستندات به صورت مرتب و شفاف باشند و کارفرما توانسته باشد نیازهای خود را به خوبی توصیف کند، بازدید میدانی از محل تولید به برآورد بهتر از شرایط واقعی کمک کننده خواهد بود.
مهندسان و تخصصهای مجرب و متعهد دکتر پی ال سی، پیش از هر گونه اقدام عملی برای آغاز پروژه، نیاز است که از کارخانه و خطوط تولید بازدید کنند و اطلاعات میدانی را به دقت جمعآوری نمایند. این بازدید میدانی به مهندسان دکتر پی ال سی امکان میدهد تا اطمینان حاصل کنند که بهترین و مناسبترین خدمات به کارفرما ارائه گردد.
4) طرحی معماری سیستم کنترل و ارائه پیشنهاد فنی
در این مرحله به حدی پیش رفتهایم که اطلاعات فنی و محیطی موردنیاز از فرآیند و کارخانه در دسترس قرار گرفته است. به این ترتیب، مهندسان ومتخصصی دکتر پی ال سی قادر خواهند بود یک پیشنهاد فنی مناسب با نیازهای کارفرما ارائه دهند. پارامترهایی که در انتخاب قطعات و معماری سیستم کنترل در نظر گرفته میشوند عبارتند از:
- نوع فرآیند و روند کاری آن
- درخواست و نیاز کارفرما
- تجربه فنی پیمانکار
- موجودی بازار داخلی
- امکان واردات قطعات
- و …
معماری سیستم کنترل نمایانگر نوع و تعداد قطعات اتوماسیون صنعتی، ارتباط آنها با یکدیگر، و نحوه ایجاد شبکههای صنعتی و سایر جزئیات است. در پیشنهاد فنی مورد نظر، علاوه بر معماری سیستم کنترل، شیوه ارتباط سیستم کنترل با اجزای فرآیند نظیر موتورها، ولوها و ابزارهای دقیق نیز بررسی خواهد شد. مطالعه پیشنهاد فنی توسط کارفرما به او این امکان را میدهد که دیدگاه بهتری نسبت به نیازهای سیستم اتوماسیون خود به دست آورد. نظرات کارفرما میتواند منجر به بازبینی و تصحیح این پیشنهاد فنی شود یا حتی نسخه اولیه آن توسط ایشان تأیید شود، که سپس میتوان به مرحله بعدی پروژه پیش رفت. اطمینان از تأیید کارفرما در این مرحله از اهمیت ویژه برخوردار است.
5) عرضه برنامه زمانبندی و پیشنهاد مالی
تعامل بین کارفرما و مهندسان و متخصصین دکتر پی ال سی در این مرحله به این شکل است که با توجه به نیازهای کارفرما و مشغله متخصصان دکتر پی ال سی ، یک برنامه زمانبندی دقیق و مشخص برای شروع پروژه و برنامهریزی مراحل بعدی پروژه توسط دو طرف تدوین میشود. اما پیش از آن، ابتدا طرفین باید در مورد جزئیات مالی پروژه به توافق برسند. هزینه یک پروژه اتوماسیون صنعتی عبارتند از:
- مخارج قطعات مثل: PLC، ماژول ها، تابلو کنترل و قدرت، قطعات low voltage، لوازم مونتاژ تابلو، درایو و سافت استارت، HMI و…
- مخارج برنامه نویسی سیستم کنترل و monitoring
- مخارج مونتاژ تابلوهای کنترل و قدرت (MCC ،Incoming و…)
- مخارج طراحی و مستندسازی
- مخارج حمل و نقل
- مخارج آموزش
- مخارج FAT
- مخارج SAT
- مخارج راه اندازی پروژه
6) بستن قرارداد و دریافت پیش پرداخت
توافقنامه میان کارفرما و دکتر پی ال سی، جزئیات فنی و حقوقی کامل پروژه را از آغاز تا پایان آن شامل میشود و به عنوان استاندارد عمل برای هر دو طرف خواهد بود. از مهمترین مسائلی که در یک قرارداد پروژه باید تضمین شوند عبارتند از:
- مشخصات کامل طرفین معامله
- مبلغ پروژه
- شیوهی پرداخت
- ضمانتهایی که پیمانکار می بایست نزد کارفرما بگذارد
- شرح وظایف دو طرف
- شرح و مفاد پروژه
- نحوهی داوری در زمان ایجاد اختلاف
- شرایط فسخ قرارداد
- تاریخ شروع و پایان پروژه
- و …
پرداخت پیش پرداخت توافق شده توسط کارفرما به معنای آغاز رسمی قرارداد تلقی شده و از پس از آن عملیات اجرایی آغاز خواهد شد.
7) دریافت لاجیک سیستم کنترل از کارفرما
هر فرآیند، به دلیل نیاز به اجرای درست و منظم خود، به یک منطق و قوانین مشخصی نیاز دارد. این منطق، نقطه آغاز و پایان فرآیند را تعیین کرده و عملکرد هر عملگر را مشخص مینماید. تأثیر فیدبک سنسورها بر روی کنترل موتورها، ولوها، بازوهای هیدرولیک و پنوماتیک و سایر اجزای فرآیند را به گونهای مشخص میکند که فرآیند مربوط به اهداف خود را به طور صحیح و دقیق به انجام میرساند. این مجموعه از وظایف جزئیات فرآیند و ارتباطات آن، که در انتهای روند از صفر تا صد پروسه توضیح داده میشود، به عنوان لاجیک یا منطق سیستم کنترل شناخته میشود.
عمدتاً در مجموعه کارفرما مهندسانی هستند که توانمندی لازم برای تدوین لاجیک مورد نیاز را دارند. در مواقع دیگر، مهندسین گروه دکتر پی ال سی به عنوان سازندگان دستگاهها و ماشینآلات مرتبط با فرآیند، لاجیک مورد نیاز را ارائه میدهند. در حالتی دیگر، متخصصین دکتر پی ال سی در زمینه اجرای اتوماسیون صنعتی، با توجه به تجربیات گذشته در راهاندازی و اتوماسیون فرآیندهای مشابه، به کارفرما در نگارش لاجیک کمک میکنند. تأیید کارفرما از لاجیک استخراج شده، به عنوان شرط لازم برای ادامه اجرای پروژه توسط دکتر پی ال سی الزامی است.
لاجیک فرآیند را چه کسانی تهیه خواهند کرد؟
کارفرما و مهندسین وی
دکتر پی ال سی به عنوان پیمانکار ماشین ساز
دکتر پی ال سی به عنوان پیمانکار اتوماسیون
8) طراحی و عرضه طرح تفصیلی سیستم کنترل
پس از تدوین لاجیک و درخواست تأیید از سوی کارفرما، مهندسان گروه دکتر پی ال سی به تکمیل طرح پیشنهادی سیستم کنترل میپردازند . با در نظر گرفتن جزئیات کاملی که جمعآوری شدهاند، آنها طرح نهایی را با دقت تکمیل و ارتقاء میدهند و اساس اجرای پروژه را با جزئیات کامل تعیین میکنند.
9) تهیه و طراحی مستندات پروژه
قبل از هر گونه اقدام، ضرورت دارد که مستندات پروژه با دقت طراحی و تهیه شوند؛ زیرا این مستندات اساس تمامی طراحیهای آتی را فراهم میکنند. به واقع، در این مرحله، یک پل ارتباطی بین اطلاعات و مستندات تحویلی از سوی کارفرما و تمامی طراحیهای آتی توسط مهندسان گروه دکتر پی ال سی ایجاد خواهد شد. مستندات مدنظر، شامل اطلاعات استخراج شده از مستندات کارفرما است که به صورت منظم و با رعایت استانداردهای مشخصی جمعآوری میشود. این مستندات شامل موارد زیر میشوند:
- فهرست ورودی خروجی های پروسه IO List
- فهرست موتورها Motor List
- فهرست ولوها Valve List
- فهرست کابل ها Cable List
- منطق فرآیند Process Logic
- فهرست تجهیزات ابزادقیق Instrument List
- فهرست قطعات مورد نیاز پروژه
اساس همه طراحی های این مرحله و تهیه مستندات، نقشه فلو پروسه (PFD) است که در مرحله 2 بوسیله کارفرما به پیمانکار تحویل داده شده است.
10) طراحریزی تابلوهای مورد نیاز پروژه
تابلوهای برق، به عنوان مرکز پویا و قلب تپنده سیستم برق یک کارخانه محسوب میشوند. این تابلوها در یک کارخانه، شامل چندین دسته و مدل مختلف میباشند. از برق ورودی با ولتاژ 20 کیلوولت پس از ترانس، تا ترمینالهای 24 ولت برای تغذیه سنسورها، تمامی اجزای طراحی تابلوهای برق فرآیند را تشکیل میدهند.
گروه بندی انواع تابلوهای برق در یک کارخانه:
Incoming Panels
PLC Panels
Marshaling Panels
Distributer Panels
Capacitor Panels
Lighting Panels
MCC Panels
و …
با توجه به اطلاعات مستندات ذکر شده در بخش قبلی، لازم است نقشه الکتریکی فرآیند بهروز رسانی و طراحی گردد. پلنهای الکتریکی تابلوهای برق در برخورداری از تمام ارتباطات و مدارهای الکتریکی از ابتدا تا انتهای یک کارخانه اهمیت دارند. به عنوان مثال، روش ارتباط الکتریکی سنسورها با ماژولهای ورودی دیجیتال و آنالوگ یا تامین تغذیه برای موتورهای الکتریکی با شینههای سه فاز تا سر تخته کلم موتور. این نقشهها با استفاده از نرمافزارهایی همچون eplan، AutoCad و یا AutoCad Electrical طراحی و بهروزرسانی میشوند.
در این مرحله، لازم است تابلوهای مورد نیاز برای پروسه را طراحی شود. این تابلوها در دو نوع سلولی (ایستاده) و دیواری بیشتر مورد استفاده قرار میگیرند، با این حال، مدل دیواری عمدتاً در پروسههای کوچک به کار میرود. طراحی صحیح و مهندسی تابلوها اهمیت زیادی دارد، زیرا میتواند به افزایش ایمنی و طول عمر تابلوها کمک کند. طراحی چیدمان و لایهبندی تابلوهای برق اصولاً با استفاده از نرمافزار AutoCad انجام میپذیرد.
11) تامین قطعات مورد نیاز در پروژه
در این مرحله از اجرای اتوماسیون صنعتی، بر اساس اطلاعات MTO (متریالز تیک اوت) جمع آوری شده در مرحله 9، باید اقدام به تأمین قطعات مورد نیاز برای پروژه اتوماسیون صنعتی نماییم. از آنجایی که اقلام اصلی در پروژههای اتوماسیون صنعتی اغلب توسط شرکتهای خارجی تولید میشوند، تأمین این کالاها میتواند از طریق منابع داخلی یا از طریق واردات از منابع خارجی انجام شود.
در واقع، گروه دکتر پی ال سی به عنوان یک پیمانکار و تأمینکننده بهطور همزمان قادر است به مشتریان خود بهترین کیفیت را با سرعت بیشتر و بهترین قیمت ارائه دهد. این گروه متخصص در ارائه اقلامی نظیر PLC و ماژولهای آن، سیستمهای پنوماتیک، انواع ابزار دقیق، درایو و سافت استارت، منابع تغذیه، کلیدهای اتومات و هوایی و ... میباشد. همچنین، محصولاتی از جمله فریم تابلوها، شینههای مسی، داکت و ریل، ترمینال و ... که توسط تولیدکنندگان ایرانی تولید میشوند، نیز در دسترس میباشند.
12) تولید فریم تابلوها
فریم تابلوها بر اساس نوع (سلولی یا دیواری)، اندازه و فضای اختصاصی بخش برق کارخانه، به علاوه با توجه به طرحریزیهای انجام شده در مرحله 10، توسط شرکتهای متخصص اتوماسیون صنعتی، از قبیل گروه دکتر پی ال سی، سفارش داده و تولید میشود.
13) مونتاژ تابلوها
در ابتدای اجرای اتوماسیون صنعتی و بر اساس نقشههای طراحی مرحله 10، فرآیند ساخت، مونتاژ، و وایرینگ تابلوها به عنوان اولین گام عملیاتی انجام خواهد بود.
گامهای مونتاژ تابلوها:
حمل و تحویل فریم تابلوها در محل کارگاه گروه صنعتی سپیانی
اندازه گذاری سینی و درب تابلو بر اساس نقشه Layout
برش و نصب Ducts and rails
نصب تمامی قطعات Trays and panel doors
Power wiring
Steering wheel wiring
مرتب سازی و فرمکاری ها
14) برنامه نویسی سیستم کنترل و monitoring
در این مرحله، تیم برنامهنویسی گرو دکتر پی ال سی به برنامهنویسی PLC و همچنین برنامهنویسی مانیتورینگ میپردازد. هر کمپانی تولیدکننده قطعات اتوماسیون صنعتی دارای یک نرمافزار ویژه برای این مرحله میباشد. آخرین نرمافزار ارائه شده توسط کمپانی زیمنس برای این کار، TIA Portal نام دارد که دو بخش اصلی برای PLC و monitoring را شامل میشود. عملیات برنامهنویسی بر اساس مستندات مراحل قبل انجام میشود. گامهای حیاتیترین برنامهنویسی PLC به شرح زیر است:
تعریف و پیکربندی hardware
تعریف و پیکربندی Network communications
تعریف سمبل ها و Tagها
نوشتن زیرتوابع برای عملکرد قسمت های گوناگون پروسه
به تحریر درآوردن توابع اصلی
برقراری ارتباط منطقی میان توابع
در نظر گرفتن شرایط ویژه و اضطراری پروسه در برنامه
شبیه سازی برنامه در محیط Simulation
حائز اهمیتترین مراحل برنامه نویسی مانیتورینگ:
تشریح و پیکربندی hardware
تشریح ارتباطات شبکه میان HMI/PC با PLC
طراحربزی اجزای گرافیکی پروسه
تشریح Tag های واسط با PLC و دیگر تجهیزات تحت شبکه
تعاریف سطح دسترسیها
تعریف و طراحریزی آلارم های پروسه
شبیه سازی برنامه در محیط Simulation
15) تست FAT
همانطور که از عنوان این مرحله آشکار است، باید یک سری آزمونها را در مورد پروژه انجام شود. FAT یا آزمون تأیید کارخانه به تستهایی اشاره دارد که باید قبل از حضور در محل کارفرما و کارخانه روی سیستم کنترل انجام گیرد. این تست با حضور نماینده فنی کارفرما در محل گروه پی ال سی انجام میشود و تابلو کنترل، سیستم قدرت، و نیز نرمافزار PLC و مانیتورینگ به شکل شبیهسازی واقعی تست و ارزیابی خواهد شد.
مواردی نظیر چک کردن آدرسهای ورودی و خروجی، بررسی شماتیکهای مانیتورینگ، اجرای حالت دستی و خودکار برنامه، از مواردی هستند که در آزمون FAT بررسی خواهند شد. پس از اتمام این آزمون، نظرات اصلاحی که احتمالاً توسط کارفرما اعلام میشوند، به متخصصین گروه دکتر پی ال سی اطلاع داده خواهد شد و تیم برنامهنویسی اقدام به اصلاح این نقاط خواهد کرد. در صورت تأیید کارفرما در همان جلسه، این تأیید به صورت کتبی اعلام خواهد شد و در غیر این صورت، آزمون FAT در جلسهای دیگر که اصلاحات مورد نظر کارفرما اعمال میشود، مجدداً انجام میشود. پس از این آزمون مجدد، کارفرما تایید کتبی را ارائه خواهد داد و مراحل بعدی پروژه قابل اجرا خواهد بود.
16) حمل تابلو به محل کارفرما
تابلوهای سختافزاری پروژه اتوماسیون صنعتی به عنوان بخش اساسی از پروژه محسوب میشوند. پس از اطمینان از صحت و کارکرد صحیح آنها و همچنین اجرای آزمونهای سختافزاری و نرمافزاری، لازم است این تابلوها به محل سایت یا کارخانه حمل و نصب گردند.
17) نصب فیزیکی تابلوها
تابلوهای برق در هر کارخانه در اتاق برق نصب میشوند. قبل از انتقال تابلوها به کارخانه، اتاق برق باید مطابق با استانداردها و نیز بر اساس نظر گروه دکتر پی ال سی به عنوان پیمانکار اتوماسیون، در بهترین و در دسترسترین نقطه در کارخانه تجهیز گردد. سپس تابلوها در اتاق برق جای گرفته و در محل نصب به صورت جانمایی قرار میگیرند.
18) نصب و راهاندازی تجهیزات ابزاردقیق
تجهیزات ابزاردقیق پروژه مانند سنسورهای دیجیتال، ترانسمیترها، اندازهگیرها، ایندیکیتورها، و دتکتورها و ... باید بر اساس نقشههای PFD و همچنین P&ID در مکانهای تخصیص یافته به آنها در کارخانه نصب شوند.
از جمله تجهیزات ابزاردقیق:
- سنسورهای مجاورتی
- ترانسمیترهای سطح LT
- ترانسمیترهای فشار PT
- ترانسمیترهای دبی FT
- ترانسمیترهای دما TT
- گیج ها
- محرک های I to P شیرهای تناسبی
- و …
19) به کار گذاشتن سینی کشی، لوله کاندوئیت و کابل کشی
در این مرحله نوبت به تعیین مسیرهای کابلکشی فرا رسیده است. سینیها و لولههای کاندوئیت و فلکسی نصب شده و کابلهای فرمان و قدرت با دقت کشیده میشوند. این کابلها به عنوان وسیله انتقال سیگنالهای ابزاردقیق، تأمین برق برای قطعات، انتقال توان به موتورها و عملگرها و ... به کار میروند. به همین دلیل، انتخاب نادرست کابلها، نصب ناصحیح در سینیهای کابل، هدایت نامناسب از لولههای کاندوئیت و لولههای فلکسی، و عدم رعایت جزییات کامل کابلکشی صنعتی ممکن است در طولانی مدت، منجر به آسیبهای جدی برروی تجهیزات و همچنین خطرات جانی برای پرسنل گردد. این عملیات کابلکشی بر اساس مستندات لیست کابل انجام میشود.
20) عملیات تست سلامت کابل ها
پس از اتمام عملیات کابلکشی و پیش از اتصال نهایی کابلها (سربندی) به زیر ترمینالهای تابلو و همچنین سربندی به تجهیزات پروسه، ضروری است که صحت کابلها چک شود. این اقدام به این دلیل است که وجود هر گونه مشکل در کابلها ممکن است پس از برقدار شدن آنها، به آسیبهای جدی منجر شود. از میان تستهای حائز اهمیت که بر روی کابلها اجرا میشود، میتوان به:
- Loop Check
- Phone Check
- Megger Check
21) سربندی تابلو و ادوات ابزاردقیق
تا اتصال زمان آن است تااتصال کابلها از هر دو سر انجام گیرد. در سر اول، اتصال به زیر ترمینالهای تابلوها و در سر دیگر، اتصال به تجهیزات عملگر و ابزاردقیق را انجام دهیم. اجرای صحیح سرسیم زدن، تگگذاری و لیبلگذاری دقیق، حفظ سلامت کابل، بهرهمندی از گلندهای مناسب، اندازهگذاری دقیق برای برش، اتصال محکم سیمها به ترمینال و اتصالات الکتریکی و... از مهمترین عوامل در فرآیند سربندی کابلها به شمار میروند.
22) کالیبراسیون تجهیزات ابزاردقیق
در این مرحله، باید تنظیمات ابتدایی ترانسمیترها و عملگرها انجام گیرد. همچنین، با استفاده از تجهیزات کالیبراتور، عملیات کالیبراسیون این دستگاهها صورت میپذیرد تا تضمین شود که تجهیزات ابزاردقیق واقعی با سیال و محصول فرآیند هماهنگ شده باشند و نقاط هدف پروسه در تجهیزات ابزاردقیق به درستی تنظیم شوند.
23) برقرار کردن سیستمها و تابلوها
در حال حاضر، وقت آن رسیده که برق اصلی به تابلوی ورودی متصل گردد. پس از آن، با فعال شدن کلید اتوماتیک یا کلید هوایی اصلی تابلو، سایر تابلوها نیز به برق وصل خواهند شد. سپس، با فعال شدن کلیدهای خودکار در سایر تابلوها، میتوان تجهیزات مختلفی از جمله منابع تغذیه، HMI، PLC، کلیدهای حرارتی و ... را روشن کرد.
24) نصب
سرورها| سیستم های monitoring | انتقال برنامه به PLC و SCADA
رایانههای صنعتی، به عنوان سرور و کلاینت در مجموعه اتوماسیون صنعتی، باید در محل مناسب خود داخل رک نصب گردند. رک سرورها باید درون اتاق کنترل و مانیتورینگ نصب شود. میز مانیتورینگ با مانیتورهای مربوطه تجهیز خواهد شد و محل استقرار اپراتورهای فرآیند مشخص میشود. تیم مهندسی گروه دکتر پی ال سی نیز به طور موقت در اتاق مانیتورینگ قرار میگیرد و سیستمهای رایانهای مرتبط با پروژه اتوماسیون را نصب و راهاندازی میکند.
در این مرحله، برنامه کنترل و مانیتورینگ بر روی PLC و سیستمهای monitoring (HMI/PC) بارگذاری میشود. همانگونه که میدانیم، یک پروژه اتوماسیون از دو قسمت نرمافزاری و سختافزاری تشکیل شده است. قسمت سختافزاری در مرحله 17 انجام شده است و نصب و راهاندازی قسمت نرمافزاری نیز در این مرحله انجام خواهد شد.
25) تست سرد خط تولید
در حال حاضر، به مرحلهای رسیدهایم که ابتدا فرمانها به پروسه کارخانه اجرا خواهند شد. تست سرد به معنای راهاندازی هرکدام از ادوات و قطعات اتوماسیون صنعتی در حالت بدون بار است. برای شیربرقیها، ترانسمیترها، سنسورها، جکها و... نیز تست سرد اجرا خواهد شد و چکلیست مربوطه تکمیل خواهد شد. نتیجه تست سرد به معنای اطمینان از کابلکشی، بررسی درستی وایرینگ درونی تابلو، اطمینان از آدرسدهی صحیح PLC و بررسی صحت عملکرد سنسورها و عملگرها است. صحت نتایج تست سرد نشانگر هماهنگی و سینکرون شدن صحیح نرمافزار و سختافزار پروژه اتوماسیون خواهد بود.
26) لوپ تیونینگ و تنظیمات ابتدایی
بعد اینکه از هماهنگی کامل سخت افزار و نرم افزار پروژه اطمینان حاصل شد می توان تنظیمات ابتدایی پروسه را انجام داد. اهم این تنظیمات عبارت هستند از:
ساماندهی set point لوپ های PID
ساماندهی set point و هیسترزیس لوپ های دیجیتال
اعمال Auto Tuning برای لوپ های PID
ساماندهی مقادیر P ،I و D
ساماندهی جریان کلید های حرارتی، اتومات، هوایی و …
ساماندهی درایوها و Soft starters
وارد کردن تنظیمات زمان و مقدار پروسه به سیستم monitoring
و …
27) تست گرم بدون محصول
در مرحله تست گرم، فرآیند خودکار تحت تست و اجرا قرار خواهد گرفت. برنامههای کنترلی یک پروژه اتوماسیون صنعتی عمدتا به دو قسمت Manual و Automat تقسیم میشوند. در مرحله 25، بخش Manual پروژه ارزیابی میشود و بخش Automatic تحت تست قرار میگیرد.
تست گرم بدون محصول به این معناست که برنامه کنترلی از ابتدا تا انتها اجرا میشود، اما هنوز هیچ سیال یا محصولی در خط تولید وجود ندارد. در این مرحله، میتوان از آب به جای سیال اصلی در خط تولید استفاده کرد تا شرایط واقعیتر مد نظر باشد و سنسورها بتوانند فیدبکهای نزدیک به واقعیت را ارسال کنند.
در این مرحله، میتوان عیوب برنامه خودکار را شناسایی کرد و اصلاحات لازم را در برنامه اعمال کرد. همچنین، میتوان کارکرد ماشینآلات و دستگاههای خط تولید را مشاهده و عیوب و اصلاحات مکانیکی و الکتریکی را شناسایی و رفع نمود.
28) تست گرم با محصول
در این مرحله، میتوان با آرامش بیشتر پروسه خودکار را در شرایط واقعی اجرا کرد. این شرایط واقعی به این معناست که محصول واقعی در فرآیند جاری تولید خواهد شد. البته با نظارت دقیق و آماده برای واکنش سریع به هر عکسالعمل.
این حقیقت را باید پذیرفت که اصلاحات در برنامه کنترلی و مانیتورینگ تا آخرین لحظه حضور تیم پیمانکار اجرای اتوماسیون، که گروه مهندسین ماهر دکتر پی ال سی میباشند، در محل کارخانه ممکن است لازم باشد. زمانی که در شرایط کاملاً واقعی و با حضور محصول واقعی، پروسه را به اجرا درآوریم، حتماً نکاتی برای بهبود، اصلاح، و رفع عیوب موارد جزیی یا کلی وجود خواهد داشت که باید به آنها پرداخته شود.
29) تست (SAT تحویل موقت)
وقتی که کارکرد کامل و صحیح سیستم کنترل برای پیمانکار تضمین شد، مرحله تحویل نهایی به کارفرما فرا رسیده است. آزمون SAT (Site Acceptance Test) به معنای ارائه سیستم کنترل نهایی است که پس از نصب و راهاندازی در کارخانه (سایت) صورت گرفته و حالا آماده تحویل به کارفرما میباشد. در این مرحله، کارفرما انتظارات خود از سیستم کنترل را به دقت بررسی کرده و عملکرد نهایی خط تولید را مشاهده و ارزیابی مینماید. اگر تماماً راضی بود، تاییدیه نهایی را به مهندسان گروه صنعتی سپیانی اعطا خواهد کرد؛ در غیر این صورت، نظرات خود را به صورت کتبی اعلام کرده و تصحیحات نهایی را درخواست خواهد کرد.
30) آموزش پرسنل
کارکنان و نیروهای فنی کارفرما موظف به دریافت سیستم کنترل از مهندسان گروه صنعتی هستند. این نیروها باید با مطالب و عملکرد سیستم آشنا شده و مهارتهای لازم برای استفاده بهینه از آن را کسب کنند. آموزش اولیه به دستگاه ها و سیستمها توسط تیم مهندسین و متخصصان گروه دکتر پی ال سی به بهترین شکل ارائه خواهد شد. این آموزشها، با توجه به سطح تخصص و تحصیلات پرسنل و همچنین نحوه درگیری آنها در فرآیند تولید، به صورت عملی و موثر ارائه میشود.
31) دوره تولید آزمایشی
به طور معمول، هنگامی که پروژه اجرای اتوماسیون صنعتی به اتمام میرسد (در پایان مرحله ۳۰)، وظیفه مهندسان گروه دکتر پی ال سی نیز به پایان میرسد. با این حال، گروه دکتر پی ال سی اعتقاد دارد که علاوه بر وظایف تعیین شده خود، باید خدمات بیشتری به کارفرما ارائه دهد. به همین دلیل یک دوره تولید آزمایشی برای کارفرما در نظر گرفته میشود و در این مدت هر گونه ایراد احتمالی توسط تیم فنی مهندسین و متخصصان گروه دکتر پی ال سی برطرف خواهد شد. آموزش پرسنل کارفرما بهطور کاملتری ادامه خواهد یافت و کارخانه نوپا با نظارت دقیق و حرفهای مهندسین و متخصصان متعهد گروه دکتر پی ال سی، به گامبرداشتن از مراحل پس از اجرای پروژه خواهد پرداخت.
32) تهیه و طراحریزی مستندات AS-BUILT پروژه و عرضه به کارفرما
اجرای مرحله As-Built به معنای اعمال اصلاحات پروژه که به صورت دستی بر روی نقشهها اعمال شده بودند، پس از به پایان رسیدن پروژه، از طریق نرمافزارهای مرتبط، این اصلاحات را در مستندات و نقشهها همچنان لحاظ کنیم و نهایتاً نقشهها را بهعنوان Final یا As-Built معرفی کنیم. نقشههای As-Built تصحیحشده، همان مستندات و پلنهای نهایی هستند که در انتهای پروژه به کارفرما تحویل داده میشوند.
33) تحویل قطعی سیستم
در این مرحله، تیم مهندسین گروه دکتر پی ال سی سیستم کنترل را به طور نهایی و بعد از اجرای تشریفات ویژه به کارفرما تحویل میدهند. با این حال، گروه دگتر پی ال سی خود را به تداوم ارائه خدمات پشتیبانی به مدت 24 ساعته متعهد می داند.
34) دوره گارانتی
در طی دوره گارانتی، گروه دکتر پی ال سی تعهد دارد که هر گونه اصلاحات، رفع مشکلات نرمافزاری، و همچنین تعمیر یا تعویض قطعات سختافزاری را انجام دهد.
35) خدمات پس از فروش پروژه های اجرای اتوماسیون صنعتی
گرودکتر پی ال سی در این بازه زمانی تعهد مینماید که خدمات عیبیابی و رفع اشکالات سیستم کنترل را ارائه دهد.
36) دوره تعمیر و نگهداری دوره ای
هر صنعت و کارخانه نیازمند یک تیم حرفهای برای تعمیر و نگهداری است. عملیات نگهداری یا PM خط تولید میتواند به دو روش انجام شود: گروهی که اعضای آن از پرسنل کارفرما هستند، یا گروهی که به صورت پیمانکاری از خارج از سازمان کارفرما فعالیت میکند. از آنجایی که متخصصین و مهندسین گروه دکتر پی ال سی با دقت بر سیستمهای خود نظارت دارند، بهترین انتخاب برای تعمیر و نگهداری، همواره متخصصین و مهندسین گروه دکتر پی ال سی میباشند. این گروه، به عنوان یکی از تخصصیترین ارائهدهندگان خدمات در این زمینه شناخته میشود.